Fine Prints
Plastic properties and innovations
May 22, 2019
A small black box zooms around, depositing thin strings of molten plastic on a growing structure, layer-by-layer. Like a regular printer, a 3D printer can fit on a desk, hums as it prints and is susceptible to clogs.
Palo Alto High School senior Ria Vora founded Vora’s Hub, a 3D printing company based on this technology, in 2016. Clients send in their 3D-printable files, and Vora uses her 3D printer to construct the desired object. Some clients use the service to make prototypes for their start-ups, and others get customized Settlers of Catan pieces for game night. Unlike other production methods, 3D printing allows for plastic to be made into shapes with intricate systems of holes, as well as highly detailed surfaces.
Vora considers the unique properties of each type of plastic such as flexibility, durability and transparency for her prints. She uses two main types of filaments: polylactic acid (PLA) and acrylonitrile butadiene styrene (ABS).
“PLA is this type of plastic that is a little bit more brittle and thin, but it is food safe and does not smell when it prints,” Vora says.
Since PLA filament is made from organic resources such as corn starch or sugarcane, it is commonly used for bioplastics like biodegradable cups, according to 3D Hubs. It prints at a lower temperature than ABS, the material used for LEGOs, which makes PLA a popular printing material. However, ABS has a higher ductility, or ability to stretch under stress. Although ABS has a higher heat resistance, it can emit harmful fumes, so it is often used industrially for prints where strength is crucial, according to Vora.
Recently, Vora has experimented with PolyWood, a type of plastic designed to appear like wood and with a similar density. She has also tried to use a water-soluble plastic known as polyvinyl alcohol (PVA) in her 3D prints. Often, when hot plastic is printed on its own, it will slump over if it is unsupported. This is where water-soluble materials come in.
The water-soluble material is printed from one of the two nozzles on the printer to make supports, and the main plastic is printed from the other. The finished product can then simply be rinsed under a faucet to dissolve the supports.
As a member of the 3D printing industry, she often attends conventions to learn more about these innovations. Vora says that there, she acquires sample plastics and meets others with similar interests.
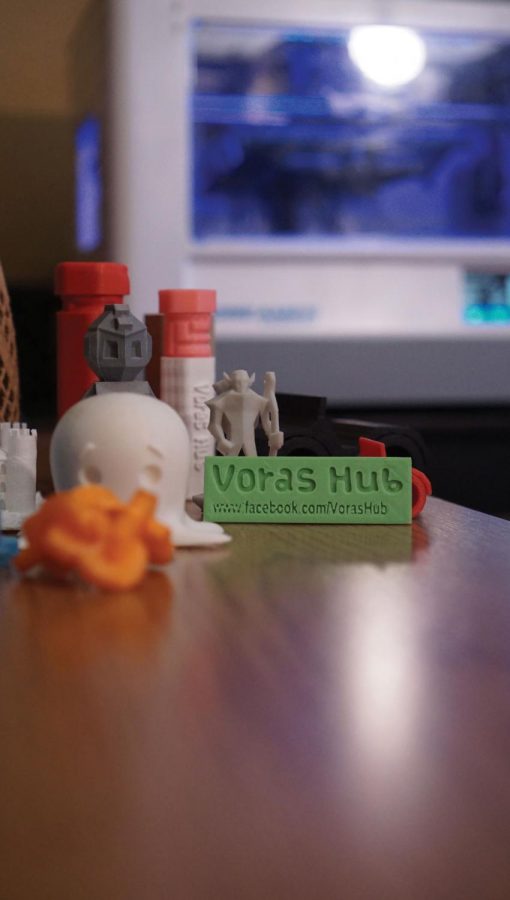
Business forward
Originally, Vora purchased the printer for personal projects and to make gifts, and she founded the printing business to recoup the cost of the printer. She works with other seniors including Zage Strassberg-Philips and Acacia Lung, who helped build her website and manage the company, respectively.
Vora’s Hub is part of a network of 3D printers called 3D Hub. People looking to print a 3D file can search for a company on 3D Hub that fits their needs. Users then rate the companies, so customer satisfaction is key.
“It’s [Vora’s Hub is] helpful for start-ups because prototyping is super expensive when they have to create a mold for every single [part],” Vora says. “Having an accessible 3D printer … makes it more affordable.”
At its peak, Vora’s Hub received up to four orders per week, but because of her increasingly hectic schedule, Vora has temporarily stopped printing.
Although Vora does not plan to continue to run her business from college, she hopes to use the skills she has learned. She plans to pursue computer science in college, and this business has helped her become comfortable with 3D printing — an important application of programming — as well as entrepreneurship skills.
“Now I know how to take any idea that I have and plug it into any 3D printer — whether it’s the one at home or one at a college campus,” Vora says.
The chance to run a business has also instilled Vora with confidence, and she has observed how the 3D printing world has grown.
“I started four years ago when there was barely any information out there about commercial 3D printing” Vora says. “The 3D printing handbook was not out, [so] I would look up how to fix clogging problems for this specific printer … and I wouldn’t find [answers]. It was so much trial and error. Now if you were to look it up, you would find a million results, and that is insane.”
• 3D printing basics •
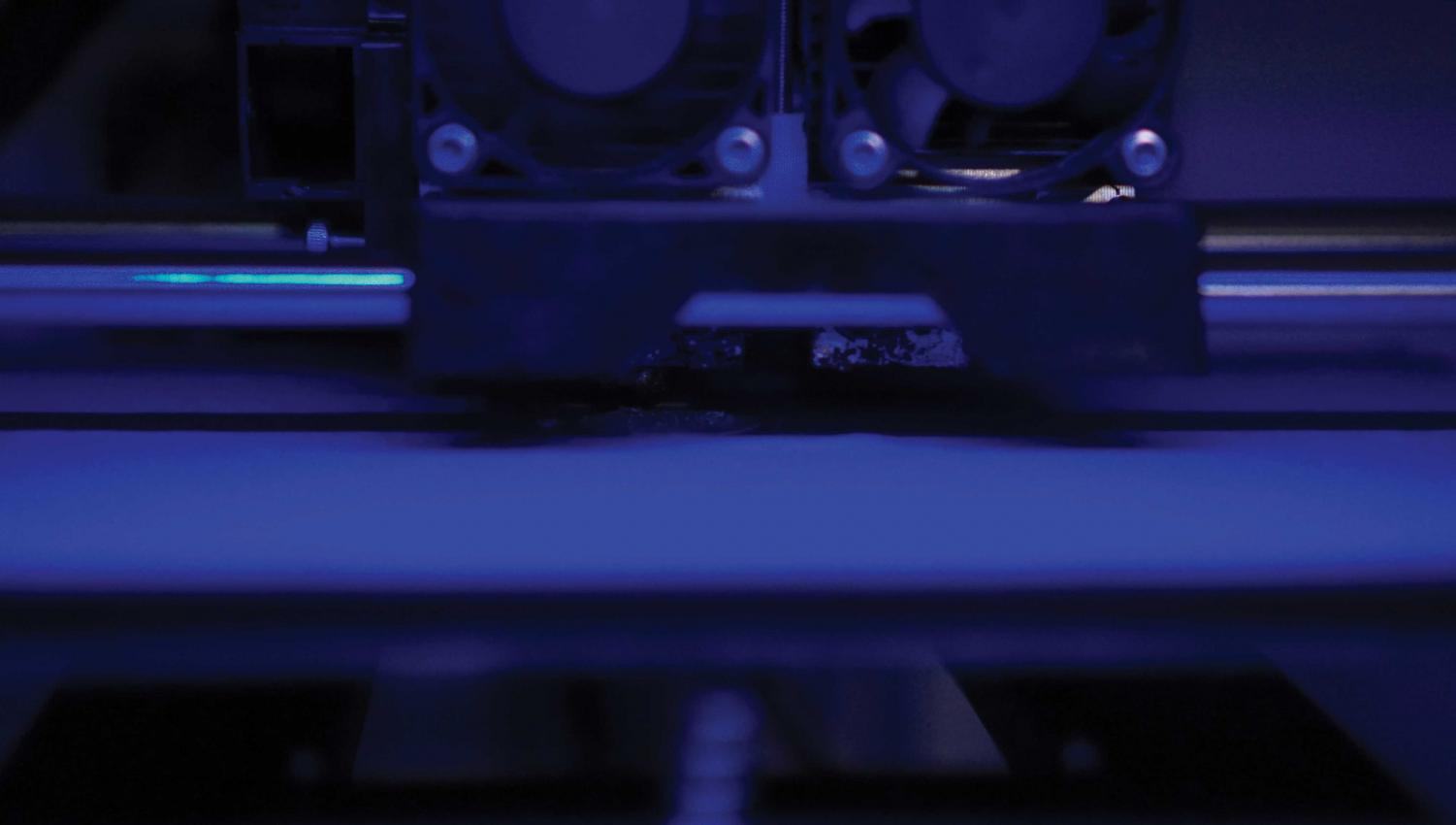
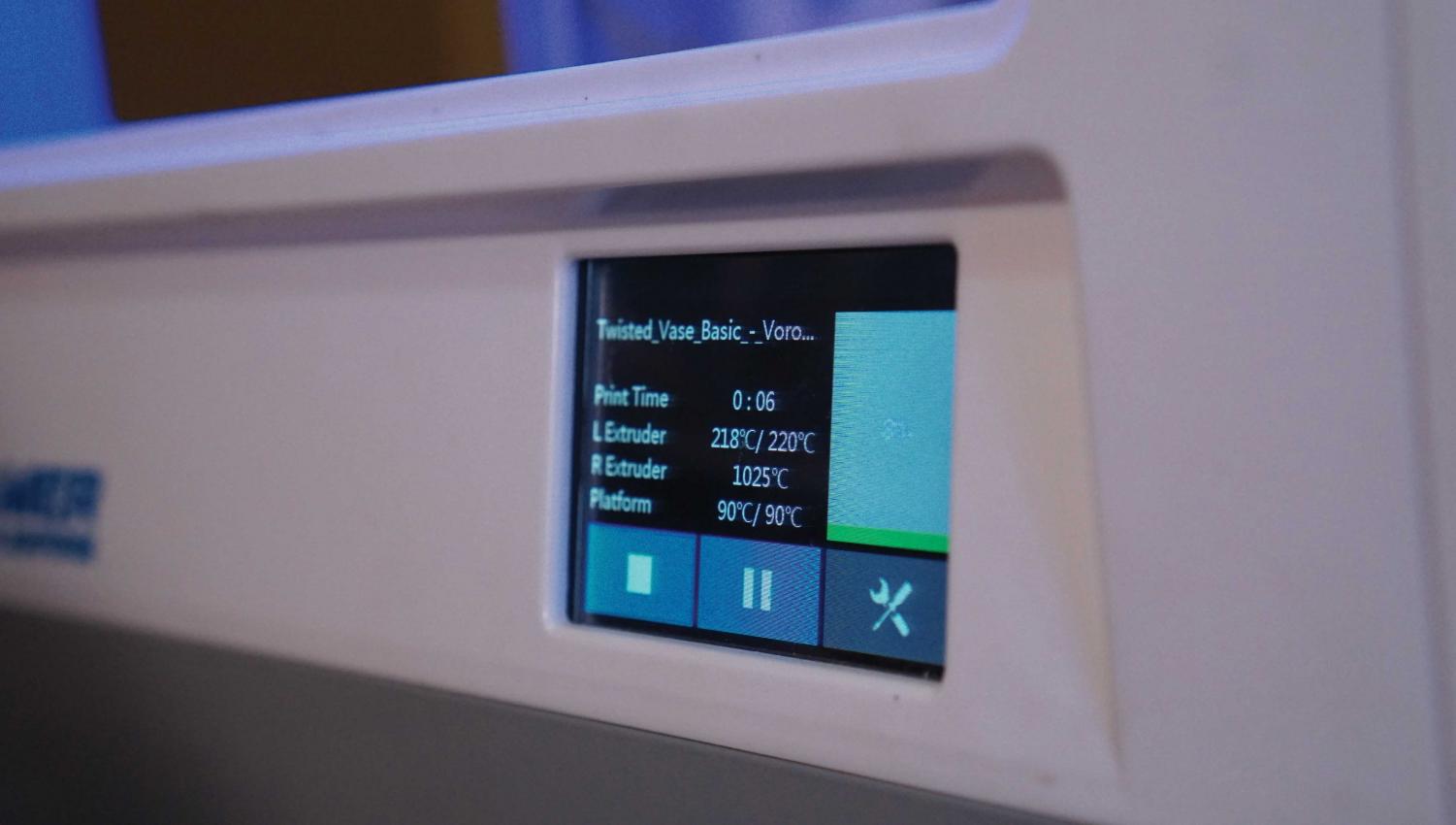
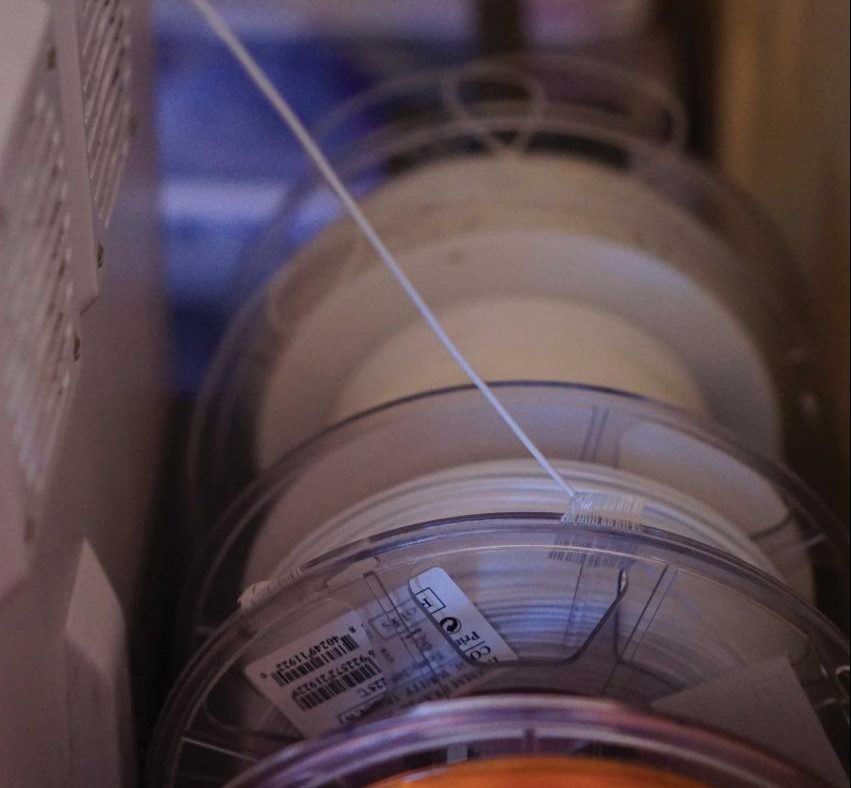
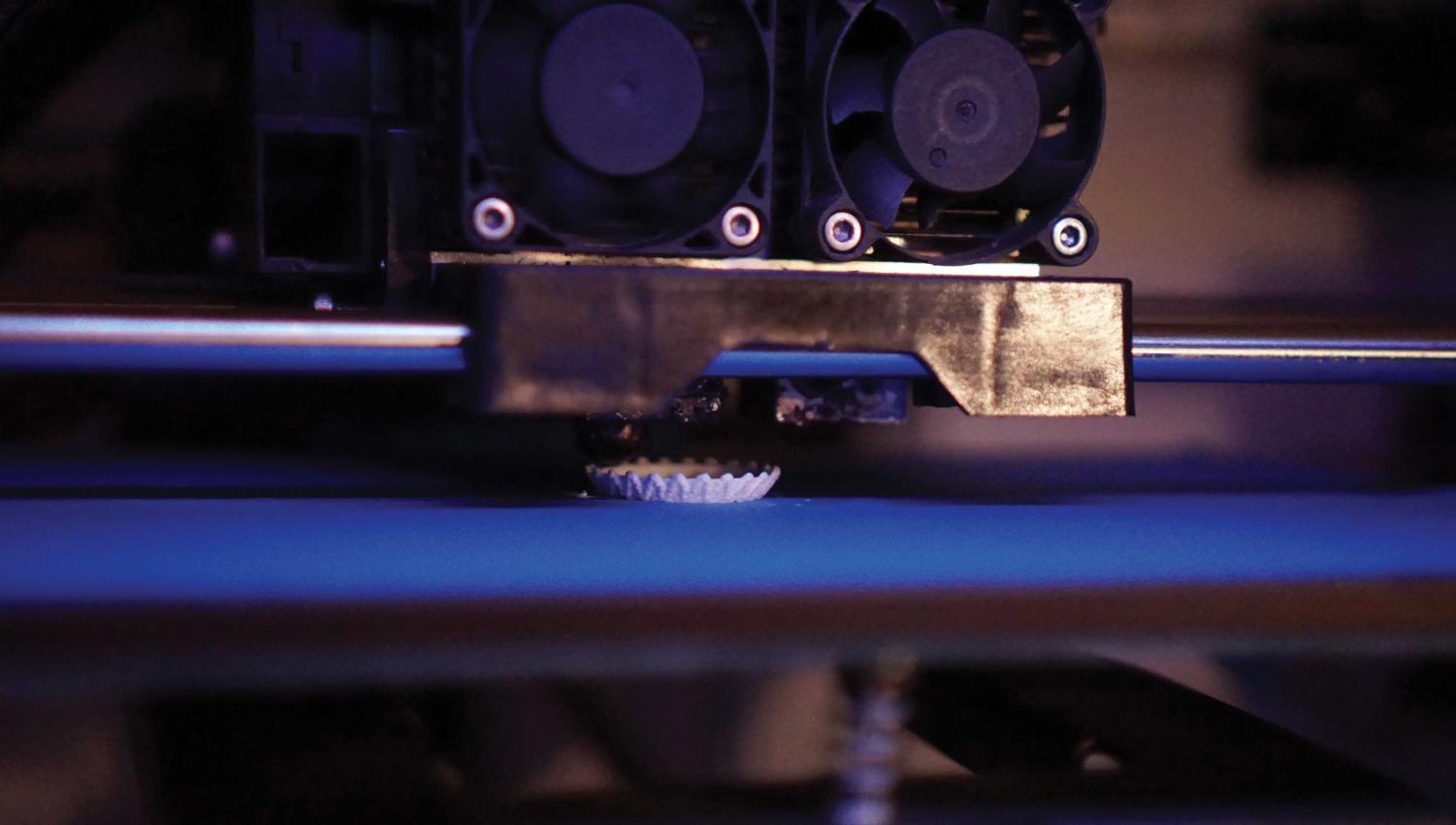